Unlocking Precision: OEM Lathe Machining Parts Manufacturers
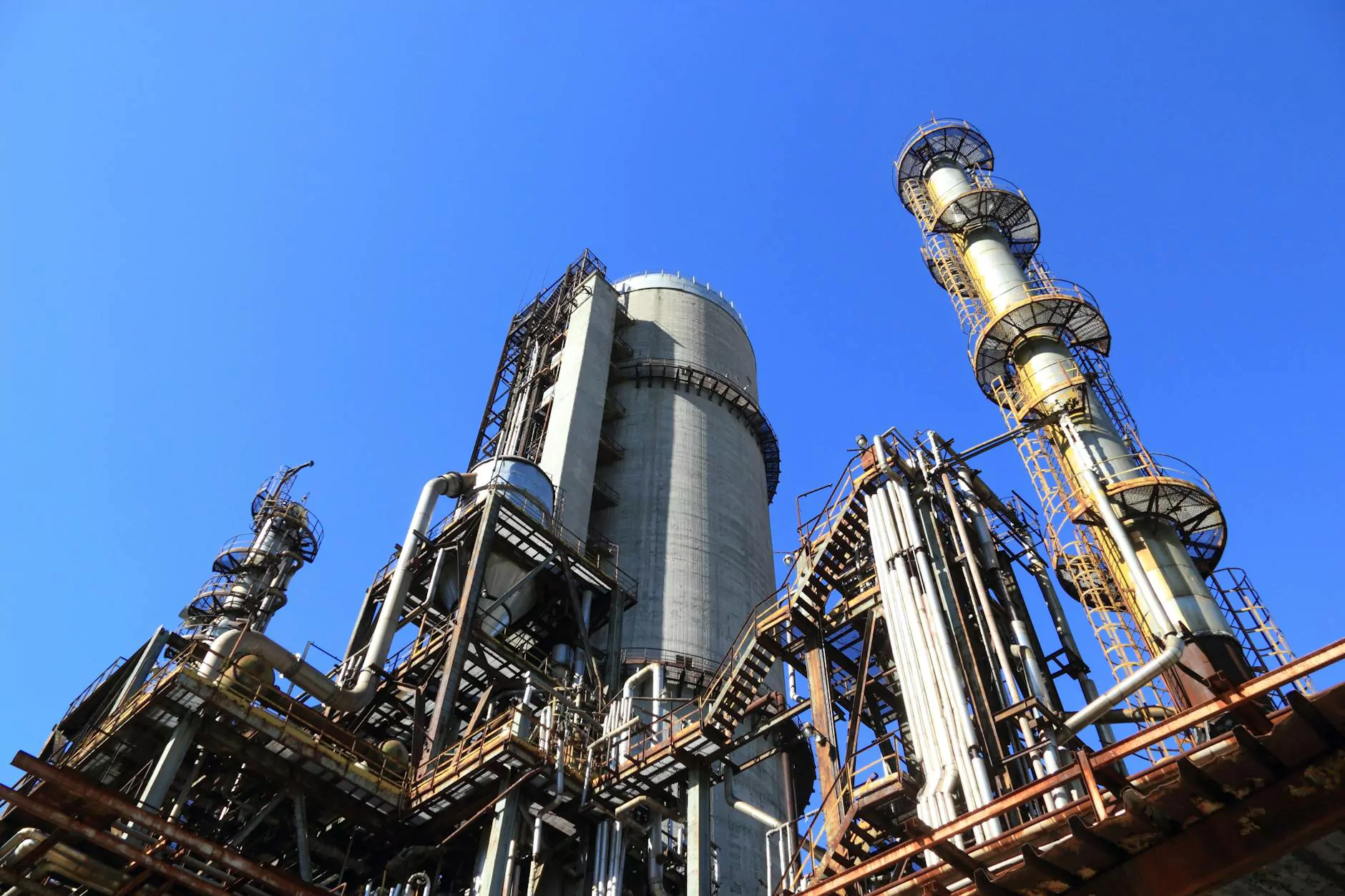
The manufacturing industry is continuously evolving, with OEM lathe machining parts manufacturers playing a crucial role in this transformation. With the increasing demand for high-quality components, businesses need to understand the importance of precision machining and how it contributes to overall efficiency and productivity. In this article, we delve deep into the nuances of OEM lathe machining, its benefits, and why partnering with the right manufacturer can make all the difference.
What is OEM Lathe Machining?
Original Equipment Manufacturer (OEM) lathe machining refers to the process of creating custom machined parts tailored for specific applications. It encompasses various activities including:
- CNC Machining: Utilizing Computer Numerical Control (CNC) lathes for automating machining processes.
- Turning: The primary operation executed on a lathe, shaping materials into cylindrical forms.
- Custom Fabrication: Designing components that meet the exact specifications of clients, ensuring compatibility and performance.
The Role of OEM in Precise Machining
OEMs are entrusted to produce parts that meet the exact specifications of their clients. This means that OEM lathe machining parts manufacturers must prioritize quality, precision, and attention to detail. By using advanced machinery and state-of-the-art techniques, these manufacturers ensure that every component meets industry standards and client expectations.
Key Advantages of Working with OEM Lathe Machining Parts Manufacturers
Several advantages underscore the importance of collaborating with reputable OEM lathe machining parts manufacturers:
- Quality Assurance: OEM manufacturers are known for their commitment to quality. They implement stringent quality control measures to ensure that every part produced meets established criteria.
- Cost-Effectiveness: Although initial costs may seem high, the long-term savings offered by durable, high-quality parts become evident over time, reducing the frequency of replacements and repairs.
- Customization: OEM manufacturers offer tailored solutions that perfectly fit your project requirements. This flexibility is crucial in industries where specifications can vary greatly.
- Technical Expertise: A good OEM lathe machining parts manufacturer should have a team of skilled engineers and technicians familiar with the specifics of your industry.
- Faster Production Times: With advanced technology and skills, manufacturers can reduce lead times, enabling quicker project launches and a more agile response to market demands.
Understanding the Process of OEM Lathe Machining
The manufacturing of components via lathe machining involves several well-defined steps. Understanding this process can help manufacturers and buyers alike to better appreciate the intricacies involved:
1. Design & Prototyping
The journey begins with designing the part. This is often achieved through CAD software, where engineers create detailed models. Prototyping allows for testing the design before full-scale production, ensuring that any adjustments can be made early in the process.
2. Material Selection
Choosing the right material is crucial in machining. Factors such as tensile strength, durability, and resistance to environmental factors play a role in selecting the correct material for the desired application. Common materials include:
- Steel
- Aluminum
- Brass
- Plastic
3. Machining Operations
Upon finalization of the design and material selection, the actual machining operations proceed. Using CNC lathes allows for high precision and repeatability, delivering components that meet tight tolerances.
4. Finishing Processes
After machining, components undergo various finishing processes. These may include:
- Graining: Enhancing surface finish for aesthetic and functional purposes.
- Coating: Applying protective coatings to improve corrosion resistance.
- Polishing: Achieving a mirror finish, enhancing visual appeal and reducing friction.
5. Quality Control
Finally, a rigorous quality control phase ensures that each manufactured part complies with customer specifications and industry standards. Techniques such as dimensional checks and non-destructive testing are employed to uphold high quality standards.
Industries Leveraging OEM Lathe Machining Parts
Several industries benefit tremendously from OEM lathe machining parts manufacturers. Here are some critical sectors:
Aerospace Industry
The aerospace sector requires components that are not only lightweight but extremely durable and reliable. OEM lathe machining plays a pivotal role in ensuring that these components meet strict regulations.
Automotive Industry
The automotive industry heavily relies on precision components for both performance and safety. Parts such as engine blocks and transmission housing are often produced using lathe machining.
Medical Devices
Machined parts for medical devices need to adhere to strict hygiene and durability standards. OEM manufacturers often produce tools and components utilized in surgical equipment that demand the utmost precision.
Electronics
In the electronics sector, OEM lathe machining is critical for crafting components used in devices that require strict reliability and functionality.
Choosing the Right OEM Lathe Machining Parts Manufacturer
Selecting an OEM manufacturer is a decision that can affect your business's success profoundly. Consider these factors:
1. Expertise and Experience
Look for manufacturers with a proven track record in your specific industry. This ensures they understand the unique challenges and requirements.
2. Technology and Equipment
The technology used by the manufacturer is crucial in determining the quality and efficiency of the produced parts. Ensure they use the latest machine tools and technologies.
3. Quality Certifications
Verify that the manufacturer meets international quality standards such as ISO 9001, which indicates a commitment to providing consistent, quality products and services.
4. Customer Service
Good communication and reliable support are essential in a manufacturing partnership. Ensure the manufacturer offers comprehensive support throughout the project lifecycle.
5. Financial Stability
Assess the financial health of the manufacturer. A stable company is likely to provide continuous service and support over time.
The Future of OEM Lathe Machining
The landscape of OEM lathe machining parts is set to evolve, driven by advancements in technology such as:
- Automation: Increased automation will streamline production processes, further improving efficiency.
- AI and Machine Learning: These technologies will assist in predictive maintenance and optimizing production workflows.
- Advanced Materials: Development in materials science may lead to lighter and stronger components, further enhancing performance across various industries.
Conclusion
In conclusion, the role of OEM lathe machining parts manufacturers cannot be overstated. As industries continue to demand higher precision, quality, and performance, partnering with a reputable manufacturer can provide significant competitive advantages. DeepMould.net is poised to assist businesses in streamlining their manufacturing processes with high-quality, custom solutions. By understanding the intricacies of OEM lathe machining, businesses can make informed decisions that will positively impact their growth and success in today’s competitive market.