Understanding Injection Molding Manufacturing
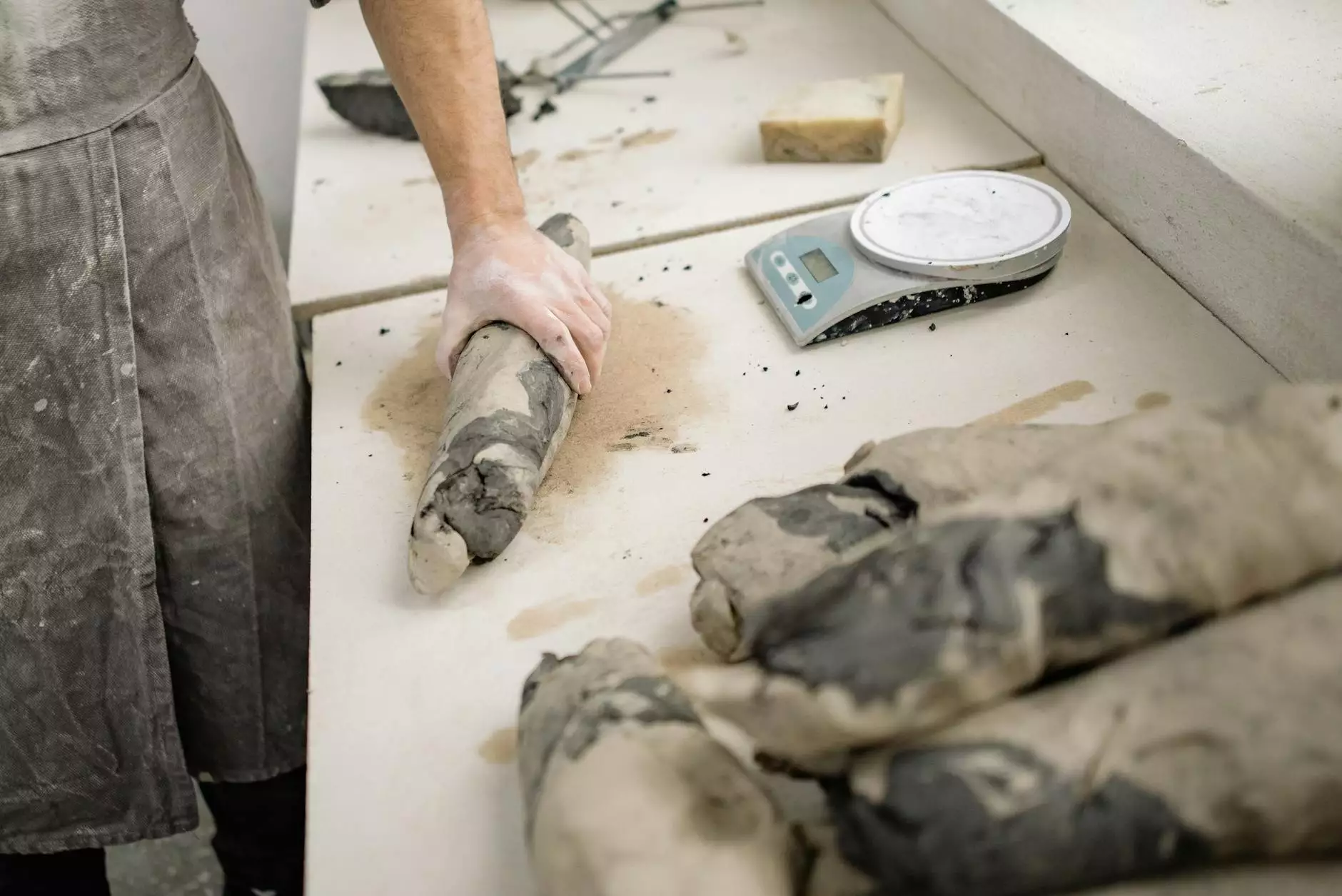
Injection molding manufacturing is one of the most prevalent techniques in the modern industrial landscape. It allows for the efficient production of intricate parts with precise dimensions, making it an essential process for various industries, including automotive, electronics, and consumer goods. This article delves into the details of injection molding, its processes, benefits, and applications, especially as it pertains to metal fabricators.
What is Injection Molding?
Injection molding is a manufacturing process whereby molten material, typically plastic or metal, is injected into a mold to create parts with desired shapes and dimensions. This process is highly efficient and can produce thousands of identical parts within a short timeframe.
The Process of Injection Molding
The injection molding process can be broken down into several key stages:
- Material Selection: The choice of material is crucial. Commonly used materials include thermoplastics, thermosets, and metals. The material's properties will determine the final part's durability, flexibility, and heat resistance.
- Injection: The chosen material is heated until it reaches a molten state and then injected into a mold under high pressure. The speed and pressure of injection are vital for achieving optimal results.
- Cooling: After the material is injected, the mold is cooled. Cooling time is critical; if not managed properly, it can lead to defects like warping or dimensional inaccuracies.
- Mold Opening and Part Ejection: Once the part cools sufficiently, the mold opens, and the finished part is ejected. Care must be taken during ejection to avoid damaging the part.
- Post-Processing: After ejection, parts might require additional finishing processes such as trimming, painting, or assembly to meet specific application needs.
Advantages of Injection Molding Manufacturing
Injection molding offers numerous advantages, making it an attractive option for manufacturers:
- High Efficiency: The process is rapid and can produce large volumes of parts quickly, making it ideal for mass production.
- Cost-Effective: Although the initial cost of molds can be high, the cost per part decreases significantly with larger production runs.
- Precision and Consistency: Injection molding produces parts with high precision and uniformity, essential for industries requiring stringent tolerances.
- Material Versatility: A wide range of materials can be used, allowing for innovation in product design and functionality.
- Reduction of Waste: The process is highly efficient, resulting in minimal scrap material when done correctly.
Injection Molding vs. Other Manufacturing Techniques
When comparing injection molding manufacturing to other techniques like machining or 3D printing, several factors come into play:
1. Machining
Machining is a subtractive process, meaning it removes material to create parts. While it offers excellent precision, it is often more time-consuming and inefficient for high-volume production compared to injection molding.
2. 3D Printing
3D printing allows for the rapid prototyping of parts but may not be as efficient for mass production. Injection molding excels in producing large quantities at a lower per-part cost.
Applications of Injection Molding Manufacturing
Injection molding has a broad range of applications across various industries:
- Automotive Industry: Used for producing interior components, bumpers, and other essential parts with complex shapes.
- Consumer Electronics: Key components for devices like smartphones, tablets, and computer casings are manufactured using this process.
- Medical Devices: Precision parts for medical devices and instruments are critical, making injection molding an essential manufacturing process in this field.
- Packaging Industry: Injection molded containers and closures are essential for ensuring product integrity and shelf life.
Challenges in Injection Molding Manufacturing
While injection molding manufacturing has many benefits, there are also challenges that manufacturers must navigate:
- Tooling Costs: The cost of designing and producing molds can be substantial, which can be a barrier for small volume production runs.
- Material Limitations: Not all materials are suitable for injection molding, and some properties may be challenging to achieve with available materials.
- Cycle Time Management: Balancing cooling times versus production efficiency requires careful attention and expertise.
Future Trends in Injection Molding Manufacturing
The future of injection molding manufacturing looks promising, with several trends shaping the landscape:
1. Automation and Industry 4.0
As manufacturers adopt Industry 4.0 principles, automation will become increasingly integrated into the injection molding process, enhancing productivity and minimizing human error.
2. Sustainable Practices
With growing environmental awareness, the industry is moving towards sustainable practices, including using eco-friendly materials and recycling scrap from the injection process.
3. Advanced Materials
Research into new materials, including bioplastics and composites, is expanding the possibilities of what can be achieved with injection molding.
Conclusion
In conclusion, injection molding manufacturing is a cornerstone of modern production techniques, providing immense value across numerous industries. With its high efficiency, cost-effectiveness, and capacity for precision, it’s no wonder that metal fabricators and manufacturers worldwide depend on this method. As the industry continues to innovate and evolve, staying at the forefront of injection molding trends will be crucial for businesses seeking to maintain a competitive edge.
For professionals in the field, understanding and leveraging the benefits of injection molding manufacturing can lead to improved product quality, greater operational efficiencies, and enhanced business opportunities. Embracing new technologies and sustainable practices will ensure continued success in an ever-changing industrial landscape.
For further insights into advanced manufacturing techniques and tailored solutions, contact Deep Mould for expert guidance and support.